Single Ply WATERPROOFING MEMBRANES The Way Forward
Upen Patel, Marketing Manager, BASF Construction Chemicals (India) Pvt. Ltd. Mumbai.
Preface
Waterproofing the concrete structures has always been a challenging task for construction industry. With the increased complexity of structures, more possibility of structural movements and settlements and growing concern on leakages in the structures has created a need for reliable waterproofing system. Current practices of rigid waterproofing barriers such as stone cladding, brick-bat koba and crystalline waterproofing has limitation if structure is designed to undergo movements during life span. Bituminous and polymer based elastic systems do enable elongations but have limiting success as they are always bonded to the substrate and does deteriorate with time. This article provides an insight to single ply synthetic waterproofing membranes which have global reputation and have gained quick acceptance in recent times in India. This article also provides insight to two of the success stories in India where the system is being employed currently.Single Ply Synthetic Waterproofing Membranes
Single-ply synthetic waterproofing membranes are widely used in Europe and North America for the last 40 years and have proven performances. The concept is to provide a watertight liner all around the susceptible building element and to ensure the right technique to install the membrane. There are various synthetic liners available for the purpose and the selection is based on the expected performance out of them in the specific situations. The single-ply synthetic liners are designed and build to the various situational needs and normally consisting of synthetic roll of fixed thickness and width and are available in reinforced with glass or polyester fibres options. Today, PVC and TPO are the most popular choice of materials for the application in the civil industry. The synthetic liners have life expectancy of 25 to 50 years v/s 10 to 15 years as offered by bituminous membranes, a single factor which made synthetic liner the popular choice in the construction sector over the years. PVC membranes are manufactured by adding plasticiser in the PVC and this limits their life expectancy in the case of direct exposure to UV and required to be protected, as plasticizers may migrate out of the membrane making the membrane brittle. Thus, PVC membranes have become chosen material for underground and buried situations while TPO, which is expensive in comparison to PVC has excellent stability in UV and available in range of colors, has become the choice for exposed roofing situations.FLAGON PVC Membranes for Underground Structures
The essential characteristics of a waterproofing liner for underground works are a high physical-chemical performance with minimum maintenance during its lifespan. Given the specific and critical nature of the work to be waterproofed, life expectancy should be measured in decades rather than years. FLAGON liners have been designed, formulated and manufactured according to specific application needs, based on a "tailor-made" philosophy. This approach ensures optimisation of results from every perspective: mechanical resistance, resistance to ageing, flexibility, ease of installation and last but not least, environmental protection.The main characteristics of Flag liners for underground works are:
- Excellent weldability
- Softness and flexibility
- High ultimate elongation (dimensional variation of the membrane when subjected to mechanical stress)
- Tensile strength (the membrane can resist tensile stress without tearing)
- Durability
- Adaptability to irregular substrates
- Maintains its integrity even in the case of structural movements or soil subsidence
- High electrical resistance
- Suitable for installation in humid places
- Resistance to static puncturing
- Resistance to dynamic puncturing
- Chemical resistance
- Resistance to bacteria and fungi
- Resistance to micro-organisms
- Resistance to roots
- Fire resistance
- Compatibility with drinking water
- Signal layer surface (essential feature to check the liner once installed–any surface damage of the liner is immediately shown by the different color appearing from the surface underneath).
The following should be considered:
- Easy weldability and workability of the material
- Compatibility with special accessories
- Ease of performing quality tests in the post-application stage (specifically, checking the welded seams).
Manufacturing Process for FLAGON PVC Membranes
FLAGON PVC membranes are produced by Co-extrusion or Spreading technique depending upon the configuration of the membrane.Co-extrusion
In this process, the mixture of material components (resins, plasticisers, stabilisers, pigments, etc.) is introduced through a hopper into a cylindrical chamber. Here it is heated up and pressed by worm screws into a co-extrusion head, where the single extruders converge, and then it is laminated in a calender. The liner thickness is automatically adjusted by electronic equipment that controls the opening of the extrusion head and of the calender. The material thus obtained is a single-layer homogeneous, non-reinforced liner, with high tensile properties and high resistance to static and dynamic puncturing. This process can also produce two-color, single-layer liners with a signal layer.Spreading
This is a manufacturing process that produces waterproofing liners in which the reinforcement becomes an integral part of the liner. At room temperature, a mixture of liquid-viscous products, called "plastisol," is spread onto a moving paper-support substrate by means of a gravity fed applicator. The mixture contains resins, plasticisers, stabilisers, pigments, etc. and determines the final characteristics of the waterproof liner. Gelation (curing) is achieved by passing the product through a series of ovens along the production line. This spreading and gelation process is repeated four times. The liners manufactured by this system are therefore composed of four differently formulated layers. Between the second and third layers, an internal reinforcement is introduced, either in polyester mesh for tensile strength or glass mesh for stability. This manufacturing system establishes a molecular bond between the four layers creating a homogenous and flexible singlelayer liner that can be combined with a thermally treated geotextile layer to improve its gripping characteristics when using adhesives or when it is laid on materials that are not chemically compatible with PVC-P. The spreading process can also produce two-color, single-layer liners with a signal layer.FLAGON TPO Liners
FLAGON TPO is a new generation synthetic liner made using an innovative formulation: EPR (ethylene propylene rubber) modified polyolefin. FLAGON TPO development has been based on experience, synergy, co-operation and manufacturing technologies:- Experience gained by Flag who, since 1963, has developed and manufactured synthetic waterproofing liners for use in the roofing, civil engineering and hydraulic sectors.
- Synergy with industry-leading manufacturers of polyolefins, who have developed and introduced these new materials to the field of waterproofing.
- Co-operation with the most qualified designers, general contractors and installation companies.
- Innovative manufacturing technologies for synthetic waterproofing materials.
Main Characteristics of FLAGON TPO Liners
The exclusive manufacturing system designed for this type of liner and its unique formulation have resulted in:- Excellent weldability
- Softness and flexibility
- Excellent dimensional stability
- High weather and UV rays resistance
- Non-toxicity
- Resistance to a wide range of chemical attacks
- Compatibility with most insulation panels, including expanded/ extruded polystyrene
- Compatibility with oxidized bitumen
- High resistance to puncturing
- Resistance to roots and microorganisms
- Adaptability to structural movements
- Environment and user friendly
- Life expectancy in excess of 25 years
- Proven installation history.
Manufacturing Process for FLAGON TPO Membranes
FLAGON EP/PV, FLAGON EP/PR liners are manufactured in UNI EN ISO 9001 certified plants and fully comply with the performance standards CEN European Standard, UNI 8629/6 – SIA 280 – DIN 16726. The raw material used to produce FLAGON TPO membranes is created by blending a mix of synthetic polyolefins and softening agents (EPR) with various additives that, through a catalloy procedure, are transformed into a moulded mass and then into granules. This combines:- Resistance to ageing, weathering and micro-biological attack
- The EPR compound gives softness and flexibility with a high resistance to mechanical and chemical influences in conjunction with the strong welding capacity of polypropylene.
The upper sand-grey color, which provides lower heat absorption, increased longevity and aesthetic qualities, represents 10-15% of the membrane thickness and the black underside, which protects against UV damage, 85-90%. The major benefit of the system becomes apparent during installation; should the membrane become damaged, the black underside is immediately detected by the contractor and simply repaired.
Application Case Study – FLAGON PVC Membrane at Delhi Metro Project Project: GTB Nagar station by Cut & Cover and ramp as part of Vishwa Viadyalaya – Jahangirpuri section.
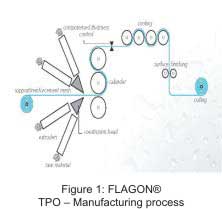
- Client: Delhi Metro Rail Corporation
- Scope of Project: Water tightness of Cut and Cover section
- Design & Construction: Senbo Engineering Limited
- Year Completed: 2006/2007 Systems used: FLAGON BFR/SL & FLAGON PROFILE W4
Project Description
The history of planning a Metro Project for New Delhi dates back to the 70's. The concept planenvisaged a network of 58 km underground and 195 km surface corridors. The total network plan contains 16 sections to be implemented in a sequence based on passenger kilometre carried per kilometre length of each section,
As in the first section of metro corridor APP membranes were used as waterproofing system and have provided enough troubles, well known for bituminous waterproofing system, summarize as under:
Moisture sensitive Overlaps cannot be tested for effective water tightness Uniform heating of membrane difficult to achieve Cannot be compartmentalized for remedial measures Non-friendly to environment and application crew Hence, designers have opted for synthetic liner which can be relied upon and takes cares of all the negatives of APP membrane systems.
The Solution Offered
Considering the water head pressure and to minimize the fire potential, 2mm thick FLAGON BFR/ SL was selected as the primary waterproof liner 250 gsm geotextile was provided as slip membrane beneath the waterproof liner. On vertical surfaces (walls) FLAGON BFR/ SL was fixed using Rondel (PVC disks) and on horizontal surfaces was kept loosely laid. 50- 75mm screed was used on the horizontal surfaces as protection layer while brick wall was used to protection the vertical installation. At the construction joints FLAGON Profile W4 was used to compartmentalize the liner and all the compartments were installed with Pipetta for injection in the future on the event of any seepage. All possible overlaps were double seam welded and tested for air leakage at 2MPa pressure for 60 and 90 seconds against the specifications and any joint found with higher than specified leakage of air pressure was re-welded. All the physical damages were reinstated using PVC patch or liquid PVC patching compound.Customers Feedback
Job was carried out to the total compliance with the QA aspects as laid by the client and consultant. Client is very much convinced about the BASF's Watertight System concept and has decided to extend the specifications for upcoming expansions in Phase II jobs.Application Case Study – FLAGON TPO Membrane at Bangalore International Airport Project: Bangalore International Airport Client: BIAL, Bangalore

- Scope of Project: Roof waterproofing of terminal building
- Design & Construction: Larsen & Toubro Limited, ECC Construction group
- Year of execution: 2006/ 2007, under execution
- Systems used: FLAGON EP/PR
Project Description
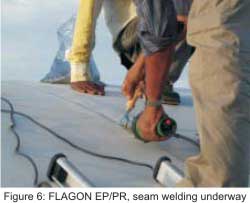
The roof of terminal building is made up of large precast segment, each of having 24 metre span and 10m length. In total there are more than 200 segments in the terminal building. The curve shape andcomplex detailing made client to choose most reliable waterproofing membrane which can be quickly installed and can last for the design period of the structure.
The Solution Offered

Conclusion
Finally local availability of single-ply synthetic waterproofing membrane, an engineered watertight system shall enable building owners and structural designers to have choice of dependable waterproofing material. The experienced application team and easy access to global experts shall enable BASF to serve the construction industry better.
NBM&CW June 2007